3D printing has evolved from a niche prototyping tool into a transformative force in manufacturing by 2025. Today, 3D printing services manufacturing 2025 are redefining production with faster timelines, reduced costs, and unparalleled customization, impacting industries from aerospace to healthcare. As of March 2025, advancements in materials, software, and service scalability are pushing this technology into mainstream industrial use. This article explores how these services are reshaping manufacturing through an FAQ-style breakdown, packed with current examples and data. Whether you’re a professional in the field or a tech enthusiast, here’s an in-depth look at how 3D printing services are driving the future of 3D printing in industry—right now!
Overview: The Manufacturing Revolution in 2025
Once limited to small-scale prototyping, 3D printing is now a cornerstone of modern manufacturing. Services like Stratasys Direct, Xometry, and Materialise are producing everything from lightweight car parts to custom medical devices at scale. A 2025 report from PwC estimates that 3D printing accounts for 12% of global manufacturing output, up from 8% in 2023, driven by faster printers and cheaper materials. Adoption is surging—Deloitte’s latest survey (January 2025) shows a 28% increase in companies using 3D printing services over the past year. So, what’s behind this shift? Let’s answer the big questions.
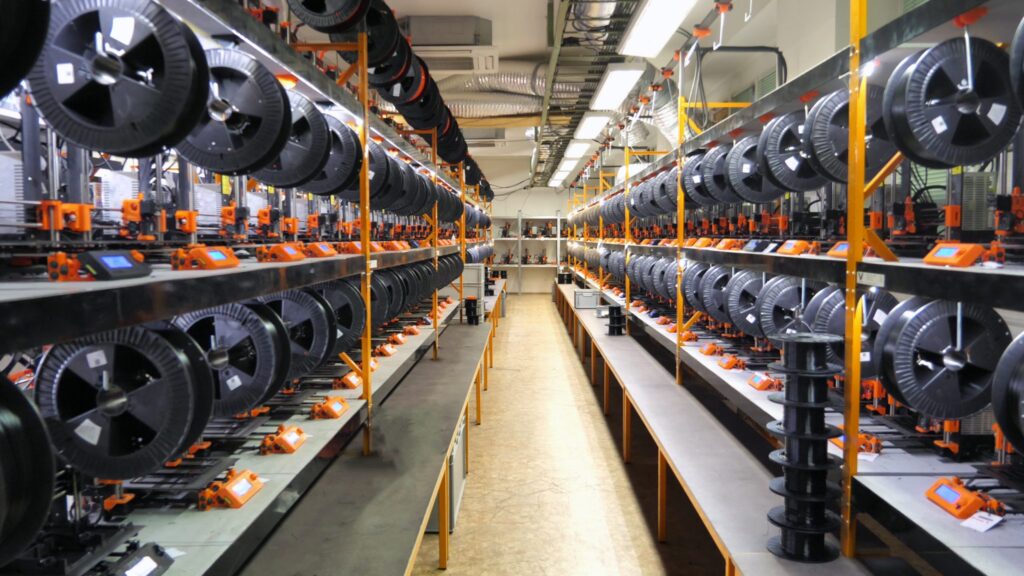
FAQ: How Are 3D Printing Services Transforming Manufacturing in 2025?
What Makes 3D Printing Services Faster Than Traditional Methods?
Traditional manufacturing relies on time-intensive steps like mold-making and machining, often taking weeks. In contrast, 3D printing services manufacturing 2025 streamline production by printing directly from digital files. Stratasys Direct, for instance, can deliver complex parts in 3-5 days, compared to 2-3 weeks for casting. A real-world example: Boeing reported in February 2025 that its new 3D-printed drone components, made via Xometry, cut assembly time by 40% compared to traditional methods. Faster print speeds—up to 100 cm³/hour on industrial printers—also play a role, per a 2025 Additive Manufacturing Research study.
How Do They Reduce Manufacturing Costs?
Cost savings come from minimizing waste and skipping traditional tooling. Advanced manufacturing 3D printing uses only the material needed, unlike subtractive methods that carve away excess. Xometry’s platform, updated in early 2025, offers instant quotes that help businesses save 25-35% on small-batch runs, according to user data. For example, a small automotive supplier in Michigan saved $50,000 in 2024 by switching to 3D-printed jigs via Materialise, avoiding costly steel molds. On-demand printing also cuts inventory costs—Ford’s 2025 sustainability report notes a 20% reduction in warehousing expenses thanks to service-based printing.
What New Materials Are Available in 2025?
Material innovation is a game-changer in 2025. 3D printing manufacturing trends 2025 highlight composites like carbon-fiber-reinforced nylon, now standard for lightweight, strong parts. Stratasys Direct introduced a new bio-based resin in January 2025, cutting production emissions by 15%, ideal for eco-conscious manufacturers. Metal printing is also booming—Markforged’s Mark Two now supports titanium alloys, used by SpaceX for rocket components, per a March 2025 press release. Meanwhile, healthcare firms are adopting biocompatible polymers for implants, with Materialise reporting a 30% uptick in medical-grade prints this year.
How Are They Improving Customization?
Customization is where 3D printing shines. Services paired with software like Siemens NX allow real-time design tweaks, producing one-off parts without retooling. In 2025, Adidas uses Xometry to print custom midsoles for its Futurecraft line, tailoring each pair to buyer specs—a process unfeasible with mass production. Medical fields benefit too: a January 2025 study from Johns Hopkins found that 3D-printed prosthetics, made via services like Stratasys Direct, reduced patient fitting times by 60% due to precise personalization. This flexibility is driving demand across industries.
What Industries Are Leading the Charge in 2025?
Aerospace, automotive, and healthcare are at the forefront. In aerospace, Lockheed Martin’s 2025 F-35 production uses 3D-printed titanium brackets from Stratasys Direct, cutting weight by 18% and costs by 22%, per their annual report. Automotive giants like BMW leverage Xometry for lightweight interior parts, with a 2025 rollout reducing vehicle fuel consumption by 10%. Healthcare is surging too—hospitals worldwide printed over 500,000 custom implants in 2024 via Materialise, a 35% increase from 2023, per a World Health Organization update. Even consumer goods are catching up, with IKEA testing 3D-printed furniture parts this year.
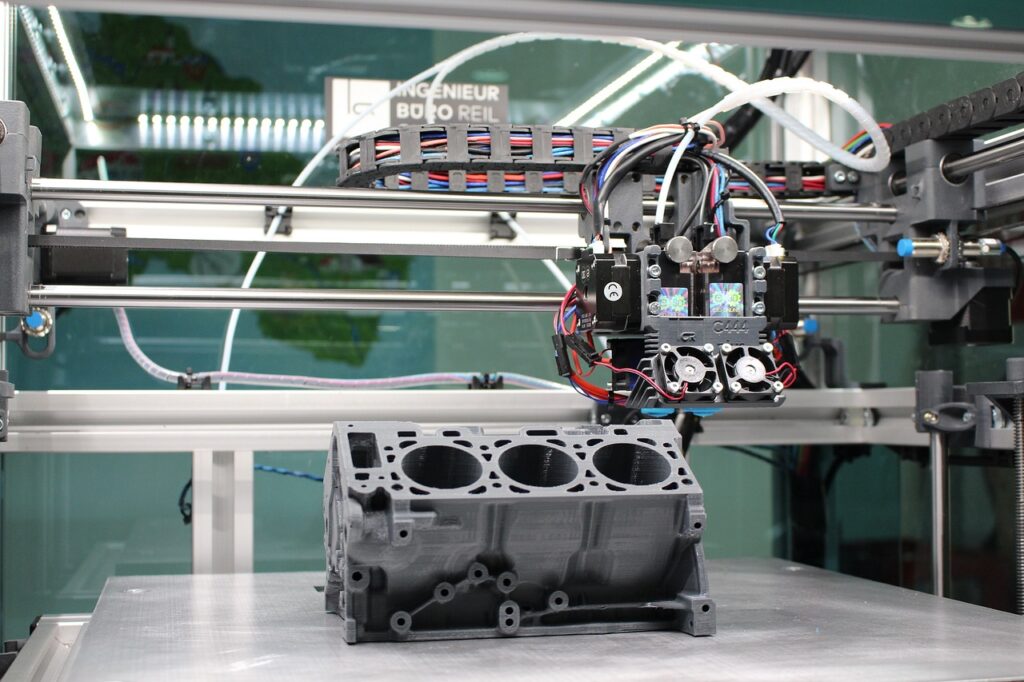
Tools and Services Driving the Change
- Stratasys Direct: Industrial-grade printing for pros. Learn more.
- Siemens NX: Design software for precision. Explore NX.
- Markforged Mark Two: A printer for tough parts. Check it out.
For deeper insights, see Forbes’ Manufacturing Trends, and IndustryWeek’s Tech Updates.
Our Articles On 3D Printing Services
- The Top 3D Printing Services of 2025: Features & Costs
- How to Scale Your Etsy Shop with 3D Printing Services
- The Cheapest 3D Printing Services for Prototyping Small Business Ideas
Conclusion
In 2025, 3D printing services manufacturing 2025 are rewriting the rules of production with speed, savings, and customization. From slashing costs to unlocking new materials, these services are the future of 3D printing in industry—and they’re here now. Whether you’re in manufacturing or just watching the trends, this tech is worth exploring. How will you tap into this revolution?