Introduction
As the demand for electric vehicles (EVs) continues to grow, manufacturers are seeking more efficient, cost-effective, and sustainable ways to improve battery production. One of the most promising innovations in this space is 3D printing in EV batteries, which is revolutionizing the industry by enabling customized designs, reduced waste, and enhanced battery performance.
With additive manufacturing, battery manufacturers can create lighter, more compact, and higher-capacity energy storage solutions, optimizing range, charging times, and longevity. This article explores how 3D printing is shaping the future of EV battery production, its benefits, challenges, and key advancements expected in the years to come.
How 3D Printing is Transforming EV Battery Production
1. Lightweight and High-Performance Battery Components
One of the biggest advantages of 3D printing in EV batteries is the ability to create lightweight and structurally optimized components. Traditional battery production methods involve casting, machining, and assembly of complex parts, which often results in material waste and design limitations.
With 3D printing, manufacturers can:
- Reduce battery weight, improving vehicle efficiency and range.
- Enhance internal structures to optimize ion flow and conductivity.
- Minimize waste by using only the necessary materials.
Researchers at Harvard University have developed 3D-printed lithium-ion batteries enabling electrodes with customizable structures.
2. Enhanced Thermal Management for Longer Battery Life
One of the key challenges in EV battery production is thermal management. Overheating can degrade battery performance and pose safety risks. 3D-printed cooling systems and battery casings allow for:
- More efficient heat dissipation, reducing thermal stress.
- Customized geometries to improve airflow and prevent overheating.
- Integration of cooling channels within battery packs for improved temperature control.
Sakuu Corporation is using 3D printing to manufacture solid-state batteries (SSBs) with enhanced cooling properties, improving safety and longevity.
3. Faster and More Sustainable Manufacturing
The conventional production of EV batteries is time-consuming and resource-intensive. 3D printing speeds up the process by:
- Eliminating the need for molds and tooling, reducing production time.
- Lowering material waste, making battery manufacturing more sustainable.
- Allowing on-demand production, reducing supply chain bottlenecks.
4. Customizable and Next-Gen Battery Designs
Traditional battery designs follow a one-size-fits-all approach, but 3D printing enables fully customizable and application-specific designs.
Innovations include:
- Structural batteries, where the battery itself becomes part of the vehicle frame, reducing weight.
- 3D-printed graphene and lithium-sulfur batteries, offering higher energy densities.
- Flexible and wearable batteries, ideal for EV interiors and alternative energy applications.
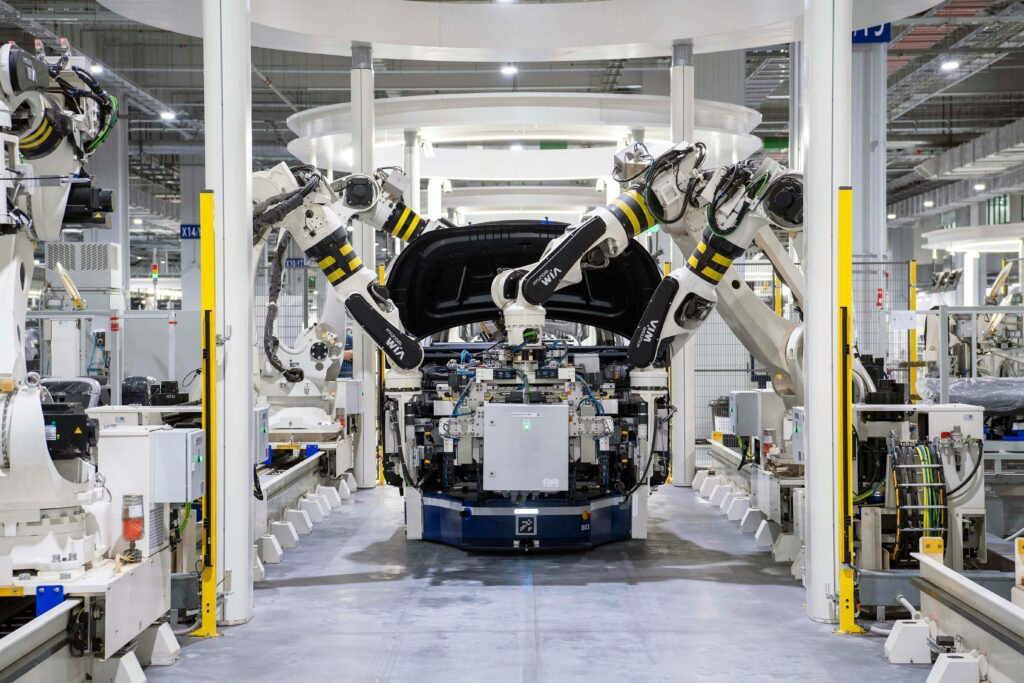
Challenges in 3D Printing EV Batteries
While 3D printing in EV batteries offers numerous advantages, there are still hurdles to overcome:
1. Material Limitations
- Battery materials (e.g., lithium, nickel, cobalt) must be adapted for 3D printing.
- Conductive inks and pastes are still in early development stages.
2. Scalability Issues
- Current 3D printing technologies are not yet optimized for mass battery production.
- High-speed additive manufacturing techniques need further refinement.
3. Cost of 3D Printing Equipment
- Industrial metal and ceramic 3D printers remain expensive.
- Cost-effective solutions for high-volume battery production are still in progress.
Future of 3D Printing in EV Battery Production
As additive manufacturing continues to evolve, the future of 3D-printed EV batteries looks promising. Key trends to watch include:
- Expansion of solid-state battery production using 3D printing for safer and more energy-dense batteries.
- Advancements in 3D-printed nanomaterials, such as graphene-based electrodes for ultra-fast charging.
- Wider adoption of 3D-printed recyclable battery components, reducing environmental impact.
- Development of hybrid manufacturing, combining 3D printing and traditional processes for efficiency.
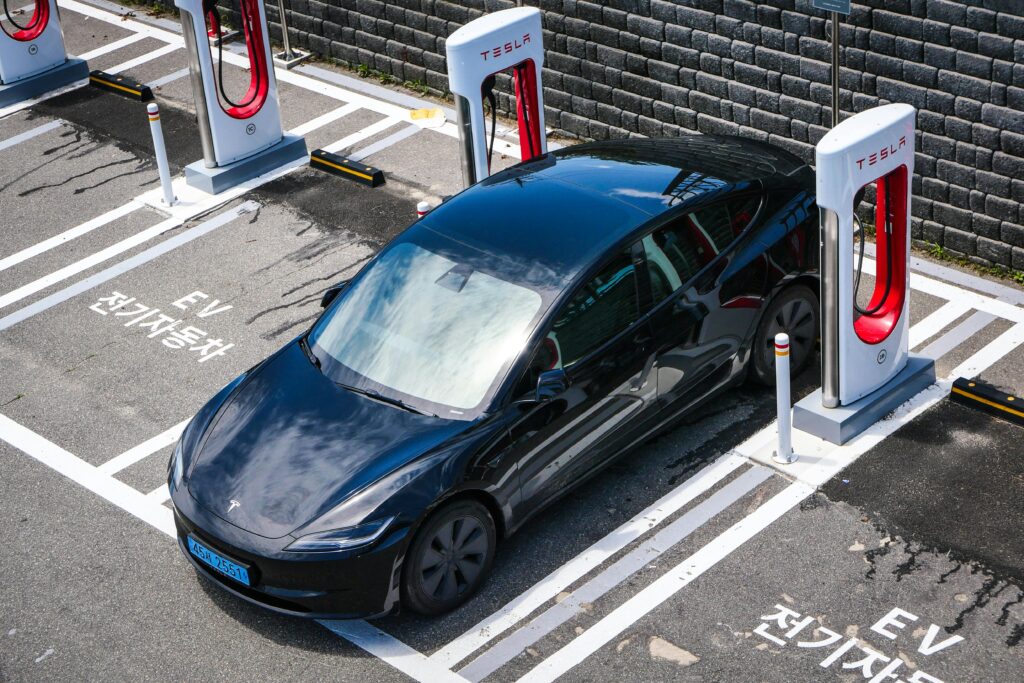
Frequently Asked Questions (FAQs)
1. How does 3D printing improve EV battery performance?
3D printing allows for lighter, more efficient battery components with improved thermal management and energy density.
2. Can 3D printing reduce EV battery costs?
Yes, by minimizing material waste, streamlining production, and reducing supply chain dependence, 3D printing lowers overall manufacturing costs.
3. What materials are used in 3D-printed EV batteries?
Common materials include graphene, lithium-ion, solid-state ceramics, and bio-based conductive polymers.
4. Are 3D-printed batteries commercially available?
Some companies, like Sakuu and BMW, are already producing 3D-printed battery components, but full-scale commercialization is still in progress.
5. Will 3D printing replace traditional battery manufacturing?
Not entirely—hybrid approaches combining 3D printing with conventional methods will likely become the industry standard.
Related Articles
- Hybrid Manufacturing: 3D Printing with Traditional Techniques
- Advancements in sustainable 3D Printing Materials: Bio-Based Filaments and Metal Powders
- 101 Innovative 3D Printing Applications Across Industries
- 3D Can 3D Printing Finally Make Solid-State EV Batteries Practical? by MotorTrend
- Additive Manufacturing For Batteries Of The Future: Will 3D Printing Transform Battery Making? by Forbes
- Why the Switch to Electric Vehicles May Boost Use of 3D Printing in Auto Manufacturing by SME
Conclusion
3D printing in EV batteries is revolutionizing the way electric vehicles are powered. With advancements in lightweight structures, improved thermal management, and sustainable battery designs, additive manufacturing is paving the way for next-generation EV batteries.
As the automotive industry continues to invest in faster, more efficient, and cost-effective energy solutions, 3D printing will play a crucial role in the future of electric mobility.